Thought Leadership: Get Lean on Scrap
Every year, manufacturers lose profits when they scrap materials and finished goods because of damage or obsolescence. In fact, the cost of scrap is far more than the cost of the material itself. Hiding behind every dollar of scrapped inventory are several more dollars lost in storage, productivity, customer satisfaction and potential revenues.
This paper reviews one of the hidden benefits of eKanban software: Scrap reduction. Download Get Lean on Scrap to learn how SyncKanban® software can help address the most common causes of scrap and accelerate your efforts in applying Lean principles in your organization. You’ll learn:
- How to use Manufacturing, Supplier and Tugger Route eKanbans to reduce defective, damaged and obsolete inventory
- Why you should pay attention to a new metric: Queue Turns
- How one manufacturer reduced 90% of their scrap in just three months
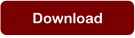